Galvanized welded wire mesh stands as a cornerstone in numerous industrial and domestic applications due to its durability, versatility,
and cost-effectiveness. Renowned for its galvanization process which involves coating the wire with a protective layer of zinc, this wire mesh offers reinforced rust resistance, making it exceptionally suitable for a variety of environments.
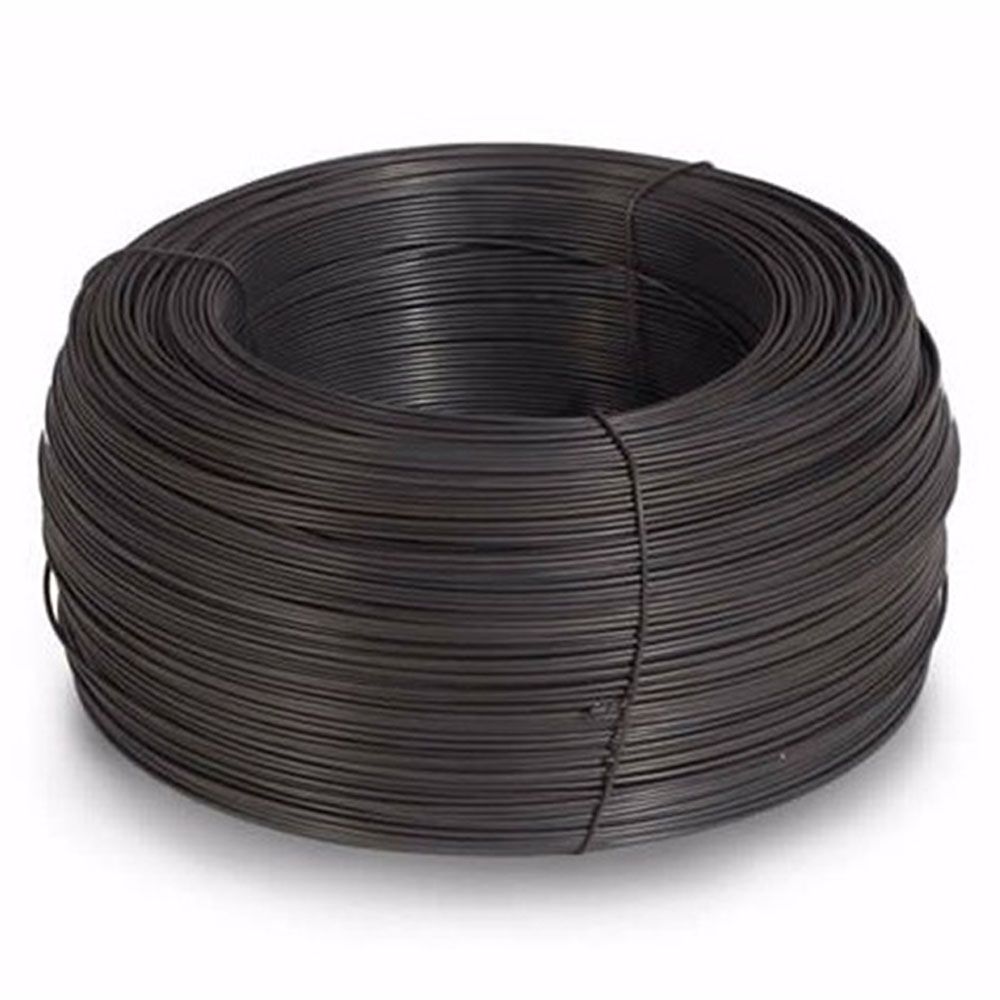
In my extensive experience working with galvanized welded wire meshes, I have consistently found that its most compelling feature is its adaptability. This product is incredibly customizable, enabling professionals to tailor widths, mesh sizes, and wire gauges to meet diverse project needs. Whether used for constructing fences, cages, grills, or architectural design elements, the possibilities are vast and centered around practical implementation.
A frequent question among industry professionals is the comparative effectiveness of galvanized welded wire mesh against its competitors. What sets it apart is its value in maintaining structural integrity in corrosion-prone atmospheres, such as coastal or industrial regions. The zinc coating performs as a sacrificial anode, meaning it will corrode before the underlying material, preserving the base metal even in harsh weather conditions. This engineered durability not only extends the life of constructions but also reduces long-term maintenance costs.
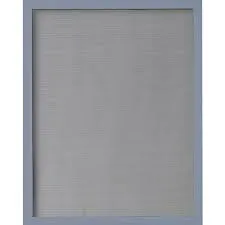
From a professional viewpoint, utilizing galvanized welded wire mesh is straightforward, enhancing its appeal across DIY enthusiasts and expert contractors alike. The ease of installation, coupled with minimal maintenance, makes it ideal for both temporary interventions and permanent installations. For small scale projects, even individuals with minimal construction experience can implement their ideas without specialized tools beyond a pair of pliers and wire cutters. This user-friendly aspect does not diminish its credibility in large-scale infrastructure projects, where its application is equally valuable.
galvanized welded wire mesh
In line with its expertise-driven developmental process, manufacturing of galvanized welded wire mesh adheres to rigorous standards. During production, top-quality carbon steel or mild steel is used, which then undergoes galvanization post-welding. This method ensures comprehensive coverage and unbroken protection against environmental factors. As a subject matter expert, acknowledging the manufacturing process’s superiority is vital for those seeking both reliable product performance and safety assurances, emphasizing the manufacturer’s commitment to quality.
Building on its credentials, galvanized welded wire mesh is recognized for its contribution to sustainability in construction. The material is fully recyclable, emphasizing an ecological advantage over alternatives that may involve composite plastics or materials harder to repurpose. Implementing recyclable materials is a critical consideration in modern construction, where environmental impact assessment is as paramount as financial evaluation.
Practically speaking, when recommending galvanized welded wire mesh in projects, credibility hinges on understanding these advantages and communicating them effectively. Ensuring clients and stakeholders appreciate the combination of cost-efficiency, versatility, and sustainability can greatly influence project outcomes. Leveraging its strengths positions businesses at the forefront of innovation in construction materials, balancing environmental responsibility with a dedication to superior craftsmanship.
In conclusion, galvanized welded wire mesh embodies engineering excellence and offers a broad spectrum of applications. Expertise-driven choices in this domain often align with evolving industry standards and sustainability goals, making it a material of choice for forward-thinking professionals. With its enduring quality and established reliability, it remains a trusted solution for myriad applications.