Understanding the Pricing Factors in Perforated Metal Sheet Manufacturing A Factory Perspective
Perforated metal sheets, with their versatility and functionality, have become a staple in various industries from construction to manufacturing, filtration systems, and even architectural design. The price of these sheets is determined by several factors that vary across different factories. This article delves into the intricacies of perforated metal sheet pricing in factories.
Firstly, the type of metal used significantly impacts the cost. Common materials include steel, aluminum, stainless steel, copper, and titanium, each with distinct properties and price points. For instance, stainless steel, known for its corrosion resistance, may cost more than aluminum due to its durability and higher processing costs.
Secondly, the perforation pattern plays a crucial role. The size, shape, and density of the holes affect the production complexity and time, which in turn influences the price. Smaller and more intricate patterns require more precision and could increase the cost.
The production process is another critical factor. Factories utilize advanced machinery for punching or laser cutting, with the latter being more precise but also more expensive. Batch sizes also impact pricing; larger quantities often lead to economies of scale, reducing the unit price.
Additionally, finishing options like painting, galvanizing, or powder coating add to the cost
Additionally, finishing options like painting, galvanizing, or powder coating add to the cost
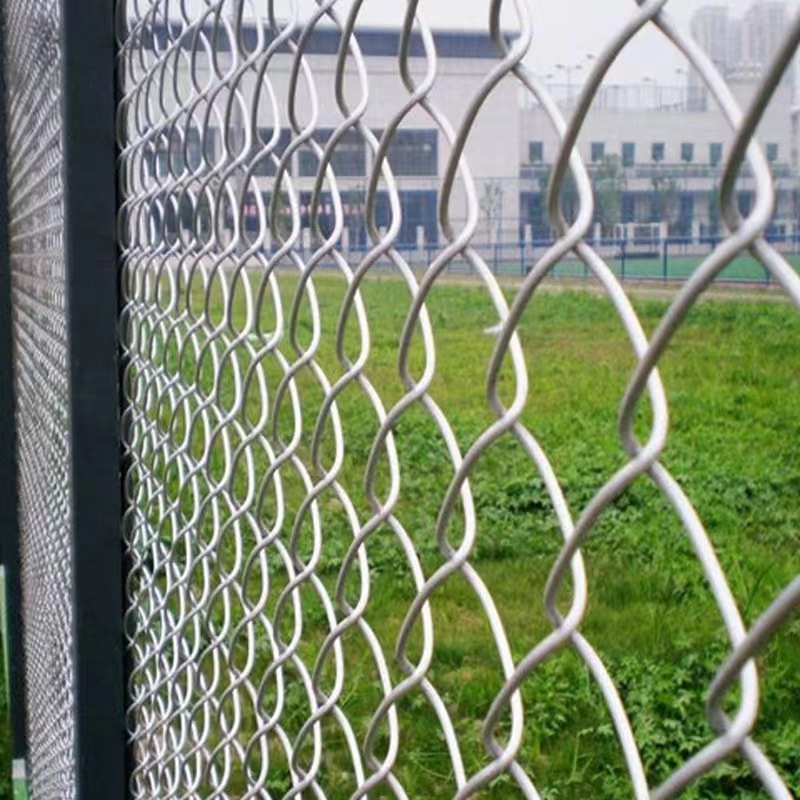
Additionally, finishing options like painting, galvanizing, or powder coating add to the cost
Additionally, finishing options like painting, galvanizing, or powder coating add to the cost
perforated metal sheet price factories. These treatments enhance the sheet's appearance, durability, or functionality, but they come at an additional expense.
Geographical location and market conditions also influence pricing. Labor costs, taxes, and transportation expenses differ globally, affecting the overall cost of production. Moreover, fluctuations in metal prices in global markets can directly impact the final price of perforated metal sheets.
Quality control and after-sales service are often factored into the price as well. Reputable factories invest in stringent quality checks and customer support, which might elevate the price but ensure product reliability and customer satisfaction.
Lastly, research and development costs are not always evident but are integral to the pricing. Continuous innovation in design and manufacturing techniques allows factories to offer better products, but these advancements need financial backing.
In conclusion, the price of perforated metal sheets in factories is a complex interplay of material choice, perforation specifics, production process, finishing, location, market conditions, and factory investments. As a buyer, understanding these factors can help make informed decisions and negotiate effectively. It's essential to strike a balance between cost and quality, ensuring that the perforated metal sheet meets the specific project requirements while staying within budget.