Custom concrete welded wire mesh has significantly gained momentum in recent years, largely due to its versatility and efficiency in construction projects. This adaptable construction material, known for its reliability and strength, caters to a broad spectrum of applications—from residential patios to massive infrastructure projects. The rise of bespoke manufacturing solutions further enhances its appeal, enabling tailored designs to meet specific project needs.
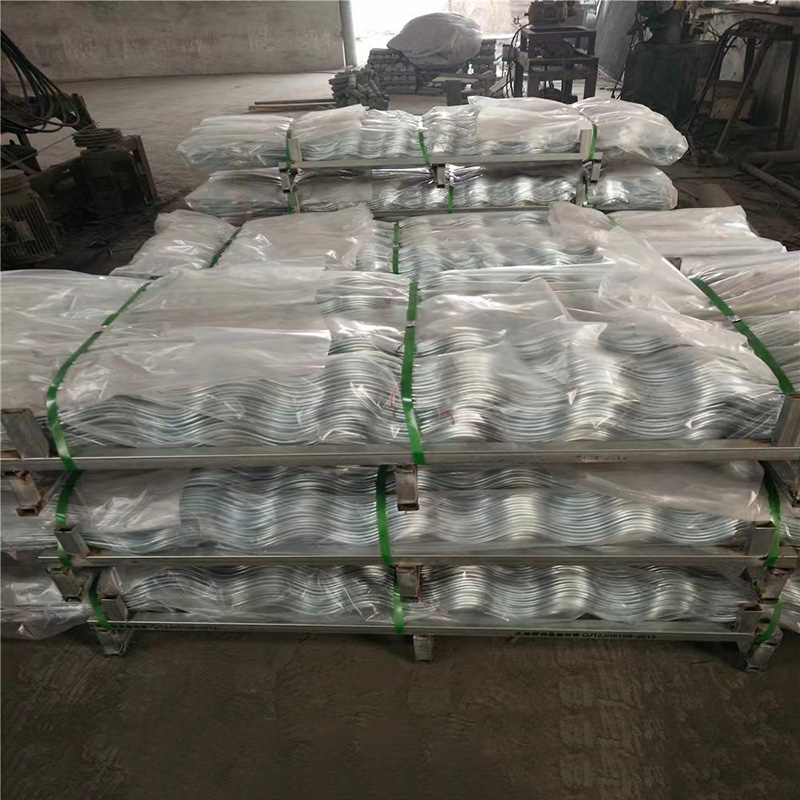
Understanding the core properties of welded wire mesh reveals why it’s a go-to material in modern construction. At its heart, this product consists of intersecting steel wires welded together at junctions to form a rigid matrix. This inherent strength results from its production process, delivering unparalleled structural integrity compared to traditional wire materials. Unlike traditional steel reinforcement, custom concrete welded wire mesh can be produced to exact specifications. This level of customization allows for optimal structural performance, ensuring every tension and compression point is adequately addressed.
One of the primary benefits of an optimized welded wire mesh is its ability to reduce installation time and labor costs. Pre-engineered panels come ready to install, minimizing onsite preparation and potential errors inherent in manual assembly processes. Experienced construction professionals constantly emphasize the dramatic reduction in turnaround times, attributing it to the precision and predictability that custom solutions provide. Consequently, projects remain within budget and meet targeted deadlines with greater efficiency.
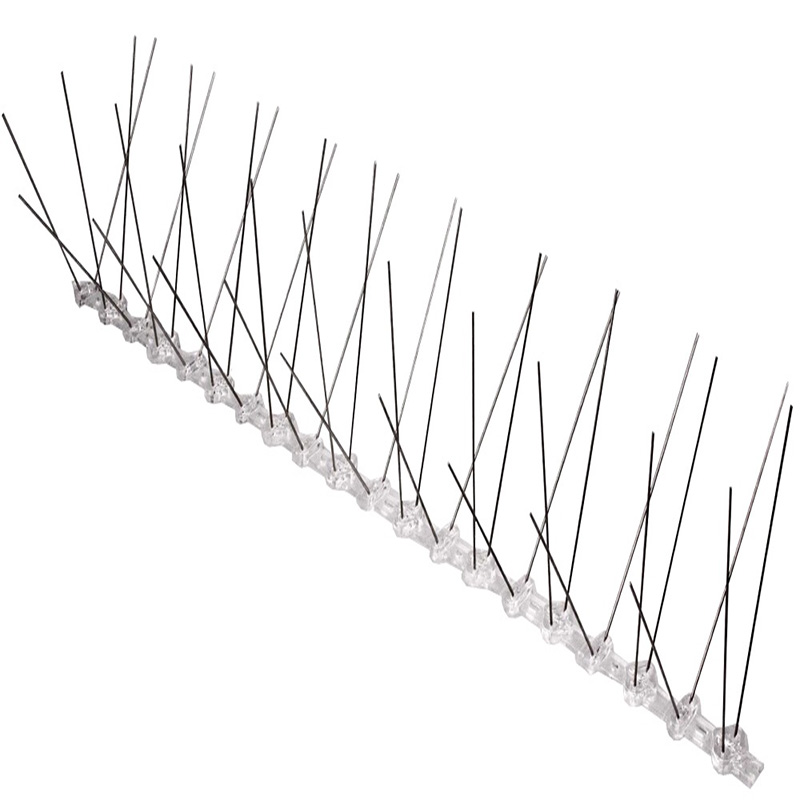
Moreover, the enduring nature of welded wire mesh makes it ideal for environments that are prone to extreme weather conditions and high stress. The robust design resists cracking and shifting over time, an invaluable feature for infrastructures subjected to constant wear and tear, such as highways, bridges, and tunnels. Custom specifications further enhance these attributes by allowing engineers to factor in environmental stresses particular to each unique site.
Expert consultation plays a vital role in leveraging the maximum benefits of custom concrete welded wire mesh. Industry specialists can provide critical insights into the selection of appropriate wire diameters, spacing, and matrix configurations. Leveraging their expertise ensures that the mesh not only meets but often exceeds the performance standards required for challenging and innovative architectural designs. Their guidance guarantees that every aspect of the mesh is tailored towards the longevity and safety of the structure.
custom concrete welded wire mesh
The credibility of custom concrete welded wire mesh is further reinforced by rigorous testing and quality assurance standards. Manufacturing facilities adhere to stringent quality control measures, ensuring that every sheet of mesh maintains consistency in tensile strength and durability. Certifications from recognized industry bodies add a layer of trustworthiness that resonates well with architects, engineers, and construction managers alike. These certifications are pivotal in maintaining industry standards and public safety.
The flexibility offered by custom concrete welded wire mesh extends beyond physical attributes; it plays a crucial role in achieving sustainable construction practices. Many manufacturers are adopting eco-friendly production methods, utilizing recyclable materials that decrease the environmental footprint. When clients opt for custom solutions, they often receive detailed information on material sourcing and lifecycle assessments, reflecting a commitment to sustainable development. As such, projects using these products often contribute to achieving green building certifications, a valued asset in today’s eco-conscious market.
Emerging trends and technological advancements also influence the evolution of custom welded wire mesh solutions. The integration of digital fabrication techniques facilitates complex design structures, pushing the boundaries of what was once possible. This advancement not only enhances the aesthetic appeal of projects but also improves accuracy and structural performance. Paired with computer-aided design (CAD) software, the possibilities for creative and functional implementations are virtually limitless.
In conclusion, custom concrete welded wire mesh stands as a testament to modern engineering and design. Its combination of strength, adaptability, and efficiency presents a compelling case for its inclusion in a wide array of construction projects. By investing in custom solutions, project managers and builders significantly improve construction outcomes, capitalizing on the material’s capacity to offer tailor-made solutions that address specific project challenges effectively. This strategic approach not only enhances functionality and aesthetic appeal but also ensures sustainability and safety are at the forefront of modern construction efforts.