Custom wire mesh rolls are an essential component in a myriad of industries, from construction and agriculture to filtration and manufacturing. These rolls are tailor-made to meet specific requirements, ensuring optimal performance and efficiency in their respective applications.
Wire mesh, also known as wire cloth or wire fabric, is a versatile material composed of woven or welded wires. The term custom refers to the ability to customize this mesh according to the customer's precise specifications. This could include variables such as wire diameter, mesh opening size, material type, roll width, and length, all of which can be adjusted to suit unique demands.
The customization process begins with an understanding of the end-use. For instance, in construction, a larger mesh size might be used for reinforcement, while a finer mesh would be suitable for architectural applications like decorative facades. In filtration, the size of the mesh openings is critical to ensure effective particle separation. Thus, custom wire mesh rolls offer a solution that is not only functional but also adaptable.
The choice of material is another significant factor. Stainless steel, for example, offers excellent corrosion resistance and durability, making it ideal for harsh environments. Copper or brass mesh may be chosen for their conductivity or aesthetic appeal, while aluminum is often used for its lightweight properties. Each material has its own set of advantages, and custom wire mesh rolls allow these benefits to be harnessed precisely where they are needed Each material has its own set of advantages, and custom wire mesh rolls allow these benefits to be harnessed precisely where they are needed
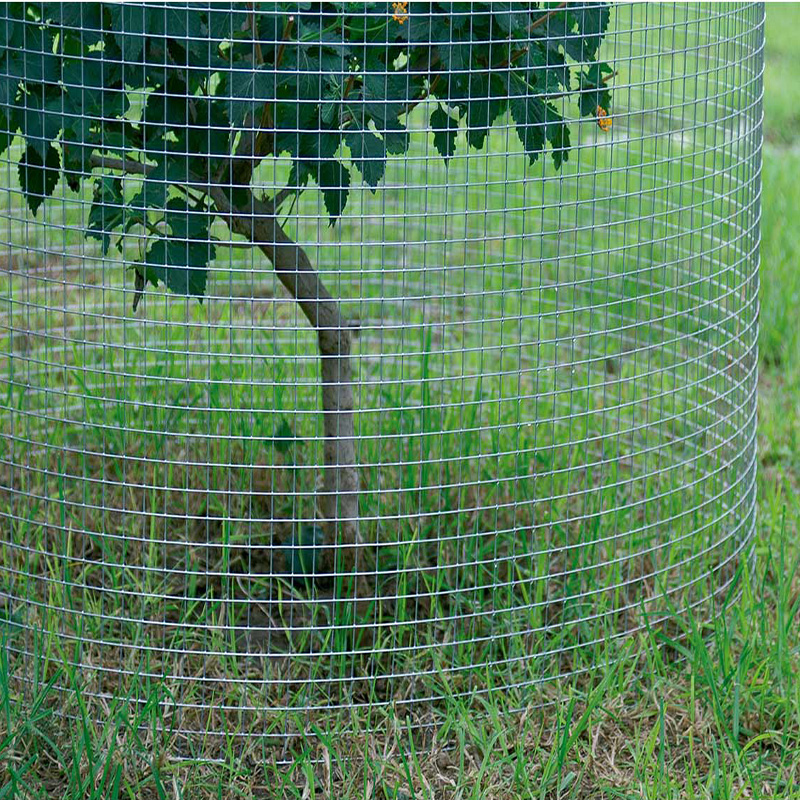
Each material has its own set of advantages, and custom wire mesh rolls allow these benefits to be harnessed precisely where they are needed Each material has its own set of advantages, and custom wire mesh rolls allow these benefits to be harnessed precisely where they are needed
custom wire mesh rolls.
The production process involves skilled technicians and advanced machinery to ensure precision and consistency. From the initial design consultation to the final product, quality control is paramount. The wires are cut, shaped, and woven or welded together to create the specified mesh pattern. The rolls are then carefully wound to maintain their integrity during transportation and storage.
Custom wire mesh rolls also offer advantages in terms of waste reduction and cost-effectiveness. By ordering only what is required, businesses can minimize overstocking and material waste. Moreover, the tailored nature of these rolls often results in a better fit and performance, reducing the need for additional modifications or replacements.
In conclusion, custom wire mesh rolls are more than just a product; they are a testament to the power of customization in meeting diverse industrial needs. They embody the perfect blend of functionality, adaptability, and efficiency, providing a customized solution for every challenge. Whether it's for sieving, screening, reinforcing, or even artistic expression, custom wire mesh rolls prove to be a valuable asset across various sectors, shaping the way we build, manufacture, and innovate.