Welded wire mesh stands as a pinnacle of innovation in construction and engineering, perfectly blending durability with practicality. This remarkable product, used extensively across various industries, is testimony to the advancement of modern materials.
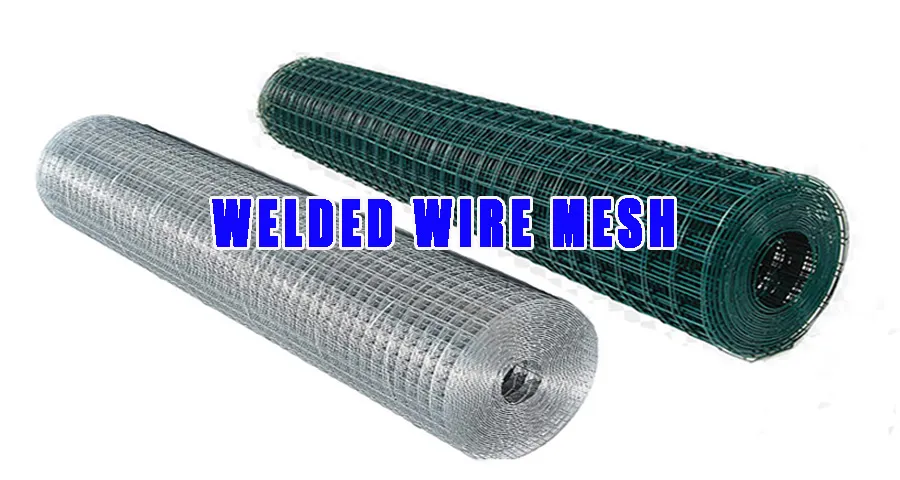
My first encounter with welded wire mesh was during a large-scale construction project where precision and reliability were critical. The project involved constructing reinforced concrete walls where traditional reinforcing methods proved to be labor-intensive and time-consuming. It was at this point that welded wire mesh demonstrated its superiority, significantly enhancing the project's efficiency and structural integrity.
Welded wire mesh, unlike its woven counterpart, is composed of intersecting wires that are welded together at their junctions, forming a grid structure. This welding process not only imparts exceptional strength but ensures that the wires maintain their relative positions, rendering the mesh ideal for reinforcement purposes. During our project, its application reduced labor costs and minimized material wastage, tearing away from the flaws of conventional mesh systems.
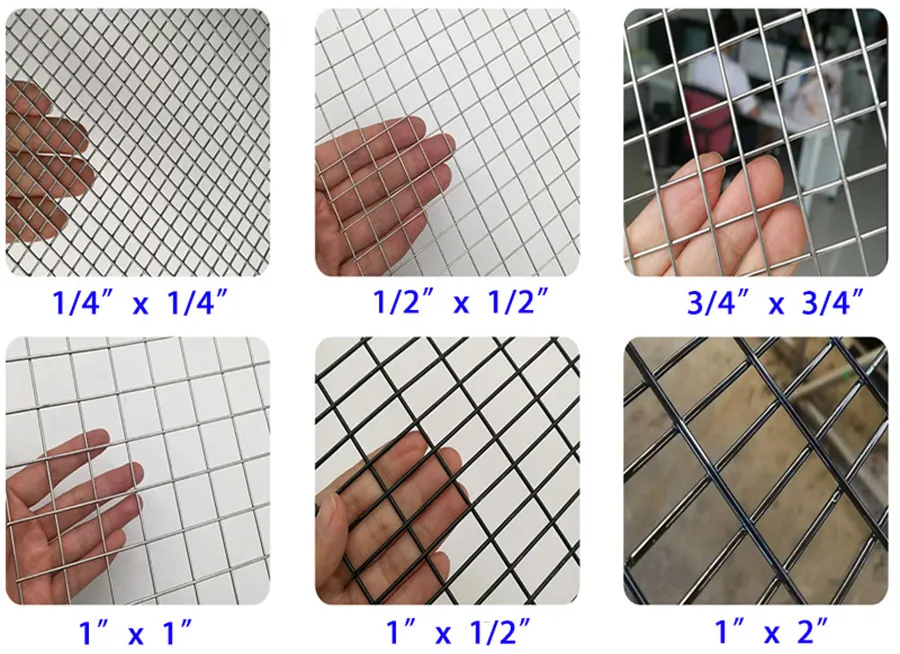
In terms of professional expertise, welded wire mesh has multifaceted uses. Construction professionals value it immensely in residential, industrial,
and infrastructure projects. Its uniform grid pattern allows for predictable stress distribution when embedded within concrete, which increases the load-bearing capacity of structures without adding excessive bulk. Moreover, its adaptability is nothing short of impressive—panels can be custom-fabricated to specific dimensions, fitting seamlessly into complex architectural designs without structural compromise.
welded wire mesh
The authoritative nature of welded wire mesh in the industry is rooted in its compliance with stringent international standards. Produced in adherence to specifications like ASTM A1064 or BS 4483, these meshes undergo rigorous quality checks ensuring their performance under varied environmental conditions. In practice, using standard-compliant welded wire mesh instilled confidence among stakeholders, knowing our construction would stand resilient against mechanical stress and environmental factors.
Trustworthiness emerges as a fundamental aspect of welded wire mesh, particularly for buyers and end-users seeking reliable construction materials. The mesh's corrosion resistance, enhanced through galvanization or epoxy coatings, ensures longevity and low maintenance overheads. In my experience, projects utilizing high-quality welded wire mesh reported fewer incidences of structural failure or the need for repairs, further solidifying trust in this material. As a preventive measure, investing in welded wire mesh with advanced protective coatings proved economically viable, saving unforeseen future costs associated with repairs.
Looking ahead, the adaptability of welded wire mesh is evolving with emerging technologies. Manufacturers are beginning to incorporate advanced materials such as high-strength steels and sustainable practices in their production processes. This not only reduces the environmental footprint but promises even greater efficiencies in construction applications. In competitive markets, the use of innovative welded wire mesh solutions can be a defining factor in project success, catering to modern demands for sustainable and robust constructions.
In conclusion, welded wire mesh epitomizes a blend of innovation, reliability, and performance in product design, establishing itself as a cornerstone in modern construction practices. From personal industry experience to adherence to stringent standards, its myriad of benefits affirm its indispensable role across various applications. As the construction landscape continues to evolve, welded wire mesh remains at the forefront of advancements, promising enduring contributions to building the infrastructure of tomorrow.