Custom galvanized wire mesh stands as a cornerstone in numerous industrial and commercial applications due to its incredible versatility, durability, and resistance to corrosion. Unlike standard wire mesh, custom galvanized options are tailored to specific needs, ensuring optimal performance in diverse environments. This specialization is not just about selecting a mesh size or gauge but involves an intricate understanding of material properties and application requirements.
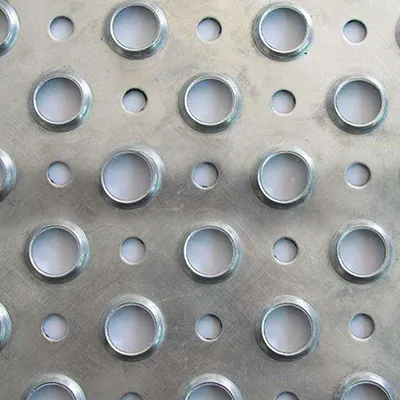
In-depth experience with custom galvanized wire mesh reveals that the customization process begins by identifying the precise needs of the application. Factors such as load-bearing requirements, exposure to environmental elements, and even aesthetic considerations play a crucial role in determining the right specifications. Expertise in metallurgy and materials science is crucial here, as the galvanization process involves coating the mesh with a protective zinc layer that enhances its strength and rust resistance.
Galvanization typically involves two methods hot-dip and electro-galvanizing. The hot-dip process, where the mesh is submerged in molten zinc, provides a thicker, more robust coating, suitable for outdoor and high-moisture conditions. This technique is often preferred for construction industries or agricultural sectors, where wire mesh may be exposed to harsh weather or corrosive agents. Electro-galvanizing, on the other hand, offers a thinner zinc layer but provides a smoother finish ideal for aesthetic applications or where a cleaner look is necessary, such as in interior design or architectural projects.
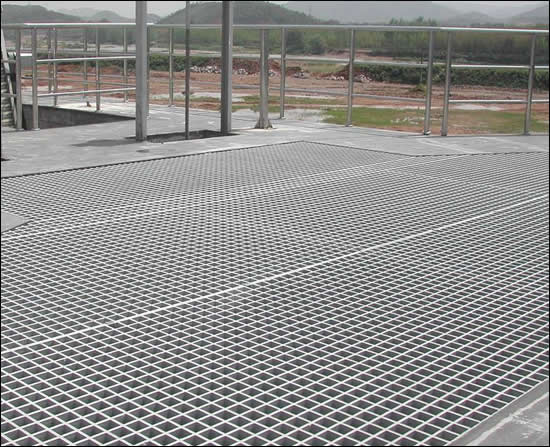
From an expert perspective, the choice between these two methods depends significantly on the application's specific demands. Those with authoritative knowledge in the field understand that while a thicker zinc coating offers extended longevity, it may not always be the most cost-effective option if the mesh isn't exposed to detrimental conditions. Trust in professional advice and proper assessment of environmental factors ensure that customers receive a product that meets their exact requirements without unnecessary expenditure.
The durability of custom galvanized wire mesh also correlates with gauge thickness. Thicker wire gauges provide increased structural integrity, imperative for projects requiring heavy-duty support. For example, in industrial operations, wire mesh must withstand significant mechanical stresses without compromising its structural formation. This mechanical property is achieved through engineering practices that balance wire diameter with the appropriate galvanization method and zinc coating thickness.
custom galvanised wire mesh
Adopting a holistic approach to custom solutions entails that environmental and mechanical criteria aren’t the only considerations. Compliance with safety standards and regulations is another critical aspect. Certifying that the galvanized mesh product adheres to regional or international standards not only boosts the product's credibility but also enhances trust among consumers. Seasoned professionals in the industry often maintain updated knowledge of such regulations, ensuring that their products are both safe and legally compliant.
Market demands are increasingly leaning towards sustainable and eco-friendly practices. In response, innovations in galvanizing techniques aim at reducing environmental footprint by minimizing zinc waste and embracing recycling. These sustainable advancements underscore the commitment to protecting the environment without sacrificing product efficacy, aligning with global efforts towards achieving more eco-conscious industrial practices.
Furthermore, customization allows for innovation beyond utility by integrating design into functionality. Businesses, especially those involved in architecture, arts, or retail, are exploring broader applications of wire mesh in creative domains. The ability to customize ensures not only performance optimization but also aesthetic enhancement, fulfilling dual purposes of utility and visual appeal.
Feedback from long-term users of custom wire mesh products often cites reliability and peace of mind as primary advantages. The assurance that the product will perform effectively over extended periods, regardless of environmental challenges, establishes it as an indispensable resource across varied industries. This resilience leads to reduced maintenance costs and product replacements, optimizing operational efficiency and contributing to project cost management.
To encapsulate, custom galvanized wire mesh epitomizes the confluence of advanced metallurgical expertise and practical application knowledge. Its ability to meet specified needs with precision makes it an invaluable resource for industry professionals seeking robust, long-lasting, and adaptable solutions. Expertise in this field not only ensures the creation of superior products but also fosters a relationship based on reliability and trust between the supplier and the end-user, solidifying its role in today’s industrial landscape.