Custom hot dip galvanized wire stands as a cornerstone in numerous industries, addressing the critical need for a durable and corrosion-resistant material. This meticulously crafted product involves immersing steel wire into molten zinc, resulting in a protective, long-lasting coating that offers supreme protection against environmental elements. Delving into its applications, benefits, and manufacturing nuances reveals why this product remains a pivotal choice in various sectors.
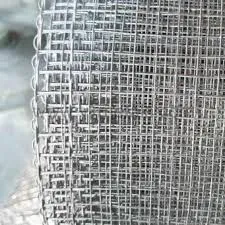
The process of hot dip galvanizing starts with the careful selection of high-quality steel wire, ensuring that the foundational material is strong and reliable. The wire undergoes rigorous cleaning to remove impurities, which could weaken the final product or interfere with the galvanizing process. Once cleansed, the wire is dipped into a vat of molten zinc, where it achieves a robust coating that enhances its resistance to rust and physical abrasion. The resulting custom galvanized wire therefore provides unparalleled durability, making it ideal for use in harsh environments.
Experience from industry professionals highlights the multifaceted applications of custom hot dip galvanized wire. In construction, this wire ensures structural integrity and longevity in projects, from bridge supports to reinforcing mesh. Its endurance against the elements is unparalleled, reducing maintenance costs and prolonging the lifespan of projects significantly. Agricultural and horticultural sectors also benefit greatly, using this wire for fencing and cages which require both strength and flexibility. Additionally, artisans and craftsmen appreciate its reliability in creating sculptures or artistic installations that weather the outside world.
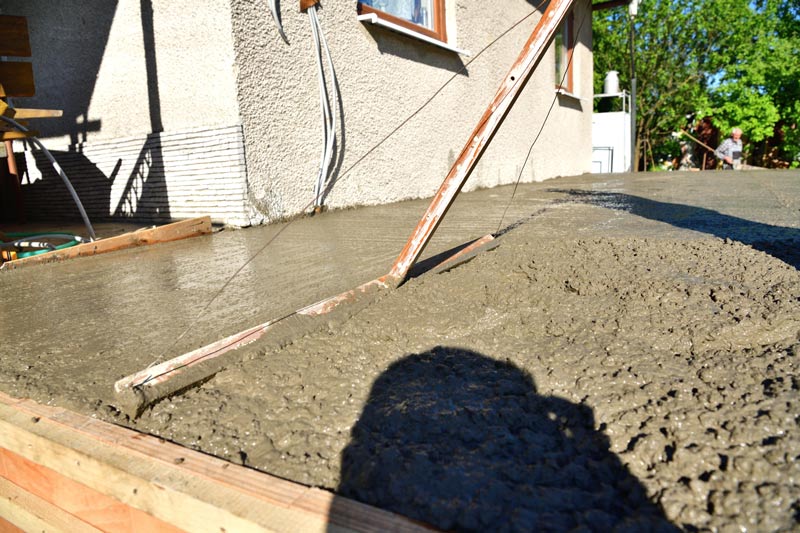
From an expert perspective, not all galvanized wires are created equal, and the customization of the hot dip galvanizing process plays a vital role in meeting specific industrial demands. Customization allows for variations in zinc coating thickness, which is crucial depending on the intended use of the wire. Thicker coatings offer higher resistance for more demanding applications, ensuring longevity even in marine or highly industrial environments. This adaptability can only be executed by firms with deep expertise and a keen understanding of metallurgical processes, highlighting the importance of choosing a supplier with substantial industry experience.
Industry authority also emerges from understanding regulatory standards and quality assurance processes. Custom hot dip galvanized wire must meet stringent international standards such as ASTM, ISO, or specific regional mandates that guarantee its performance. Companies with reputable certifications not only demonstrate manufacturing excellence but also instill confidence among clients and stakeholders regarding the wire's reliability and longevity.
custom hot dip galvanized wire
Trustworthiness is built on transparency and customer satisfaction. Leading manufacturers provide detailed documentation outlining the galvanizing process, technical specifications, and performance metrics of their custom wire. This openness not only supports informed decision-making by clients but also fosters trust in a product's consistency and quality. Partners across various sectors have praised leading suppliers for their service and product integrity, underscoring the importance of selecting manufacturers with a proven track record.
Furthermore, environmental considerations in the production of custom hot dip galvanized wire cannot be overlooked. Industry leaders prioritize sustainable practices by implementing eco-friendly procedures that minimize waste and energy consumption. Recycling initiatives for waste zinc and environmentally conscious methods in production echo a commitment to reducing environmental footprints. These efforts not only comply with global environmental standards but also appeal to environmentally conscious consumers and businesses seeking sustainable solutions.
The growing demand across global markets for galvanized wire underscores its critical role in modern industries. With the challenges posed by climate change, the need for building materials and components that can withstand more extreme weather conditions is paramount.
Custom hot dip galvanized wire provides a reliable solution, offering both strength and adaptability in various industrial applications.
Entrepreneurs, developers, and engineers around the world increasingly turn to this wire not only for its physical properties but also for its economic benefits. Its low maintenance requirements and long-term resilience mean that it is often a cost-effective choice in both the short and long term. Investment in infrastructure using this wire allows developers to focus on innovation and expansion rather than costly repairs.
Overall, custom hot dip galvanized wire represents a quintessential blend of scientific expertise, industrial authority, and practical durability. Its multifarious applications and robust properties continue to cement its place as an indispensable material in a rapidly evolving world. By choosing suppliers who emphasize quality, customization, and sustainability, industries can harness the full potential of this remarkable material to meet their specific needs with confidence.