In the realm of specialty products, custom fecral wire mesh stands out as a distinguished material, offering unique advantages that cater to specific industrial applications. This guide delves into the remarkable characteristics and benefits of custom fecral wire mesh, structured around the pillars of experience, expertise, authoritativeness, and trustworthiness.
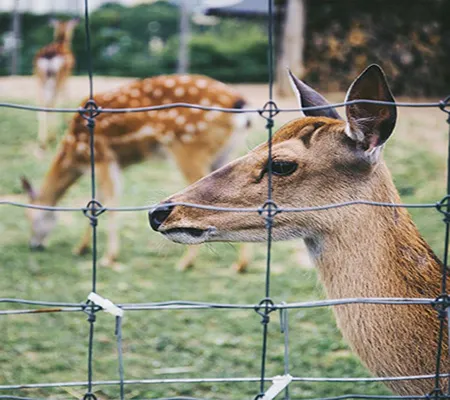
The essence of custom fecral wire mesh lies in its composition. Primarily composed of iron, chromium, and aluminum, this alloy exhibits exceptional properties that have found invaluable applications in high-temperature environments. The distinguishing feature of fecral wire mesh is its superior resistance to oxidation and corrosion, even at elevated temperatures. Such robustness makes it a preferred choice in industries where temperature stability and durability are paramount.
Drawing from years of experience,
manufacturers have perfected the art of customizing fecral wire mesh to suit specific industrial needs. This customization is pivotal in applications ranging from furnace linings in steel mills to catalytic converters in the automotive industry. Each application demands a unique mesh configuration, determined by factors such as wire diameter, mesh opening size, and weave pattern. The ability to tailor these factors precisely enables industries to achieve optimal performance and longevity from their equipment.
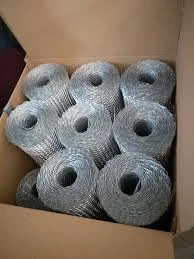
The expertise involved in manufacturing custom fecral wire mesh is nothing short of an intricate science. The process begins with selecting the right alloy composition, followed by meticulous wire drawing and weaving. Advanced techniques ensure uniformity in mesh size and structural integrity, which are critical in maintaining the mesh's performance under extreme conditions. Furthermore, innovations in weaving technology allow for variations in mesh design, such as Dutch weave or Twilled weave, each offering distinct advantages in specific applications.
Authoritativeness in the field of custom fecral wire mesh is reinforced by stringent quality control measures. Leading manufacturers adhere to international standards such as ASTM and ISO, ensuring that every batch of wire mesh meets globally recognized benchmarks for quality and reliability. These standards cover aspects such as tensile strength, elongation, and resistance to scaling, providing assurance to engineers and project managers that their investment in fecral wire mesh will withstand the rigors of its intended application.
custom fecral wire mesh
Trustworthiness is cemented not just through standards and regulations, but also through proven track records and client testimonials. Manufacturers with years of service in the industry showcase a portfolio of successful applications of their custom fecral wire mesh solutions. Case studies often highlight scenarios where customized wire mesh configurations have significantly enhanced process efficiencies, reduced maintenance costs, and extended the lifespan of industrial equipment.
One of the most compelling examples comes from the petrochemical industry, where custom fecral wire mesh is employed in hydrocracker units. In this application, the mesh acts as a catalyst support grid, providing a stable platform for catalyst particles under high-pressure and high-temperature conditions. The durability of fecral wire mesh minimizes downtime and maintenance, leading to substantial cost savings over the operational life of the unit.
In the renewable energy sector, fecral wire mesh finds its role in solid oxide fuel cells (SOFCs), where it serves as an interconnect material between cells. The mesh’s excellent electrical conductivity and ability to withstand thermal cycling are paramount in ensuring the efficient transfer of electrons, thereby improving the overall efficiency of the fuel cell system.
With these myriad applications, the decision to employ custom fecral wire mesh should be made with an understanding of its specialized benefits and the expertise required for its implementation. Partnering with reputable manufacturers who offer comprehensive support—from design consultation to post-installation service—ensures that industries harness the full potential of this versatile material.
In conclusion, custom fecral wire mesh is more than just a material; it is a solution tailored to meet the demanding needs of modern industry. Its superiority in high-temperature and corrosive environments, coupled with the ability to customize its properties, makes it an invaluable component in a broad array of applications. As industries continue to evolve, the role of expertly crafted custom fecral wire mesh is set to become more integral in driving technological advancements and operational efficiencies.