The flat razor wire, a formidable barrier against unauthorized intrusion, is a product that requires precise manufacturing processes. In the realm of security fencing, the flat razor wire manufacturer plays a crucial role in shaping the effectiveness and reliability of perimeter protection systems.
Manufacturers of this specialized wire face numerous challenges in their quest to produce a consistently high-quality product. The flat razor wire's sharp edges must be uniformly spaced and honed to a fine edge, ensuring that it presents a significant deterrent to any would-be intruders. This demands meticulous attention to detail during production, from the selection of raw materials to the final cutting and shaping processes.
One key aspect of flat razor wire manufacturing is the material selection. High-tensile stainless steel or galvanized steel is commonly used due to its durability and resistance to corrosion. Once the appropriate material has been sourced, it undergoes a series of rigorous treatments including drawing, leveling, and cutting to achieve the desired thickness and width. The next critical step involves creating the sharp edges through a process called razorizing. This entails cutting precise angles into the metal strip to form the distinctive blade-like projections that give the flat razor wire its name.
After the razorizing process, the wire undergoes a cleaning stage to remove any burrs or sharp edges that may have formed during cutting
After the razorizing process, the wire undergoes a cleaning stage to remove any burrs or sharp edges that may have formed during cutting
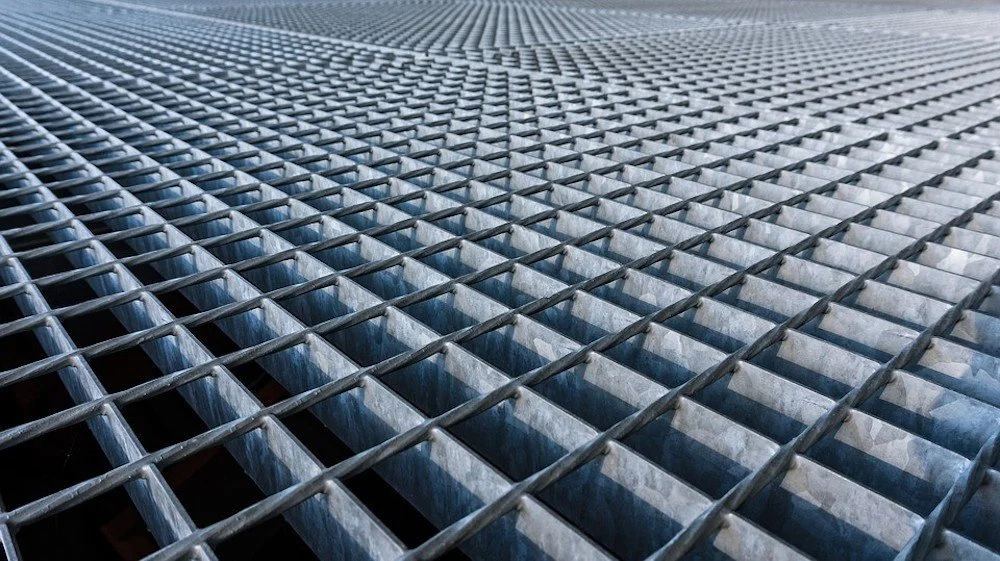
After the razorizing process, the wire undergoes a cleaning stage to remove any burrs or sharp edges that may have formed during cutting
After the razorizing process, the wire undergoes a cleaning stage to remove any burrs or sharp edges that may have formed during cutting
flat razor wire manufacturer. It is then ready for the finishing touches, which may include additional treatments such as electropolishing or coating with protective layers to enhance its longevity and weather resistance.
Quality control is an integral part of the manufacturing process. Each batch of flat razor wire must undergo rigorous testing to ensure that it meets international safety standards. These tests can range from simple visual inspections to more complex mechanical stress tests designed to simulate the wear and tear the wire might experience over time.
Moreover, ethical considerations are becoming increasingly important in the manufacturing sector. Companies that prioritize sustainability and worker welfare often gain favor with consumers and B2B clients alike. As such, manufacturers are compelled to maintain humane working conditions, fair wages, and environmentally friendly practices throughout their supply chains.
In conclusion, the production of flat razor wire is a specialized field that demands a blend of technical expertise and commitment to quality. Manufacturers who excel in this area are those who balance precision engineering with a dedication to ethical business practices, ensuring that the end product is not only effective but also reflects responsibility towards people and the planet.