The Art and Function of Perforated Metal Panels A Journey into the Factory
Perforated metal panels, a versatile and innovative architectural material, have been increasingly adopted in various industries due to their aesthetic appeal and practical applications. These panels, often seen adorning facades, interiors, and even acoustic systems, are meticulously crafted in specialized factories that blend technology with artistry.
The perforated metal panel factory is a hub of precision engineering and creative design. It begins with the selection of raw materials, typically steel, aluminum, or stainless steel, each chosen for its durability, strength, and resistance to corrosion. These metals are then transformed into sheets, ready for the next phase - perforation.
The perforation process itself is a marvel of modern manufacturing. High-tech machinery, equipped with computer-aided design (CAD) and computer numerical control (CNC), punch holes into the metal sheets according to predetermined patterns. These patterns can range from simple circular or square shapes to intricate geometric designs, offering architects and designers endless possibilities for expression. The size, shape, and spacing of the perforations are carefully calculated to achieve specific functionalities, such as light filtration, ventilation, or sound absorption.
Once the perforation is complete, the panels undergo additional processes like edge finishing, surface treatment, and powder coating
Once the perforation is complete, the panels undergo additional processes like edge finishing, surface treatment, and powder coating
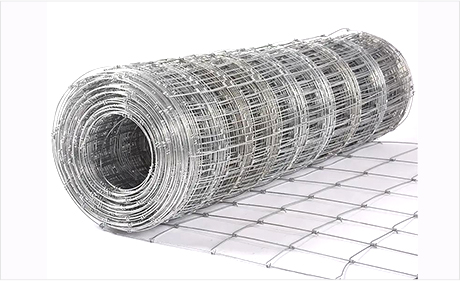
Once the perforation is complete, the panels undergo additional processes like edge finishing, surface treatment, and powder coating
Once the perforation is complete, the panels undergo additional processes like edge finishing, surface treatment, and powder coating
perforated metal panel factory. Edge finishing ensures safety and longevity by removing sharp edges, while surface treatments like galvanizing or anodizing enhance the panel's resistance to environmental factors. Powder coating, on the other hand, adds a layer of color and protection, allowing the panels to blend seamlessly into their surroundings or make a bold statement.
In the final stage, quality control takes center stage. Each panel is meticulously inspected for accuracy, consistency, and overall quality. This rigorous process ensures that the finished product meets the stringent standards of the construction and design industry.
Perforated metal panel factories, therefore, are not just production lines; they are incubators of architectural innovation. They bring together the science of engineering, the precision of technology, and the creativity of design to create products that are both functional and visually stunning. From the bustling cityscape to the tranquility of a park, perforated metal panels, born in these factories, continue to reshape our built environment, proving that form and function can indeed coexist harmoniously.