Understanding PVC Coated Wire Manufacturing in Modern Factories
In the world of industrial materials, PVC coated wire has become an indispensable element due to its versatility and durability. This specialized wire, with its polyvinyl chloride (PVC) coating, offers a perfect blend of strength, resistance, and aesthetic appeal. The production process in a PVC coated wire factory is a testament to modern manufacturing techniques and precision engineering.
A PVC coated wire factory typically begins with the selection of high-quality raw materials. This includes galvanized steel wire, which serves as the core, and PVC resin, which forms the protective coating. Galvanized steel, with its corrosion-resistant properties, ensures the wire's structural integrity, while PVC resin adds an extra layer of protection against environmental factors such as moisture, UV rays, and extreme temperatures.
The first step in the production process is wire drawing. Here, large steel coils are fed into specialized machines that pull and stretch the metal to the desired diameter. This not only reduces the size of the wire but also increases its tensile strength.
Next comes the coating phase, often referred to as 'wet process' or 'dry process'. In the wet process, the wire is immersed in a bath containing liquid PVC compound, then heated to form a solid, adherent layer. In the dry process, the wire is coated with a PVC powder, which is then fused onto the wire through a process called electrostatic spraying and subsequent curing In the dry process, the wire is coated with a PVC powder, which is then fused onto the wire through a process called electrostatic spraying and subsequent curing
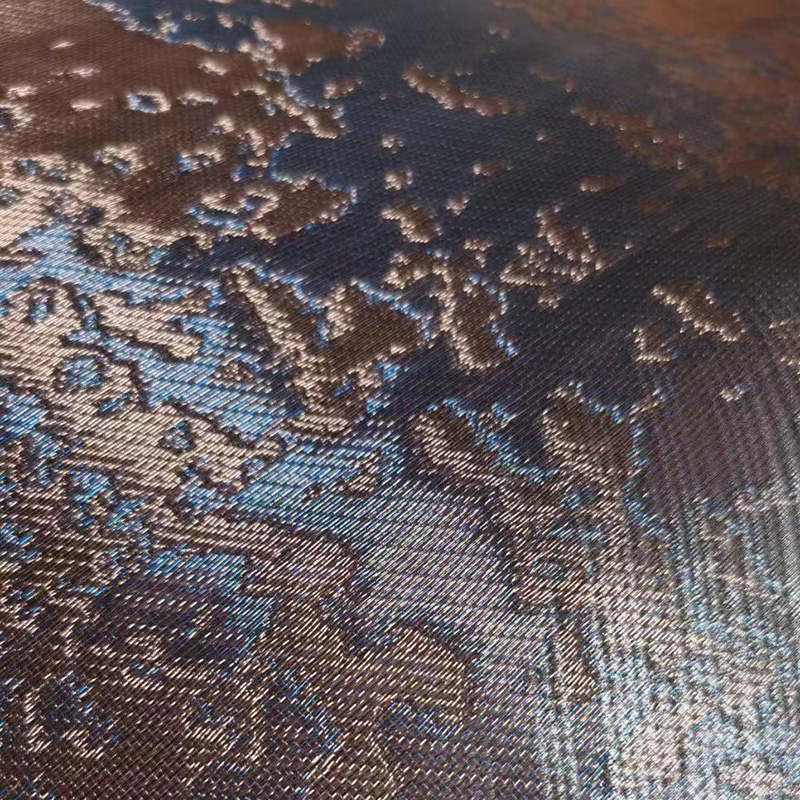
In the dry process, the wire is coated with a PVC powder, which is then fused onto the wire through a process called electrostatic spraying and subsequent curing In the dry process, the wire is coated with a PVC powder, which is then fused onto the wire through a process called electrostatic spraying and subsequent curing
pvc coated wire factory. Both methods ensure a uniform and robust coating.
Quality control is a critical aspect in any PVC coated wire factory. Advanced testing equipment is used to check the thickness, adhesion, and flexibility of the coating, ensuring it meets industry standards and client specifications. Any wires that don't meet these standards are discarded, ensuring only the best quality product leaves the factory.
Once the wires pass the quality checks, they are wound into reels or spools, ready for packaging and shipment. These finished products find applications in various industries, from construction and agriculture to manufacturing and landscaping, where their durability and flexibility are highly valued.
In conclusion, a PVC coated wire factory is a hub of technological innovation and precision engineering. It is a place where science and technology merge to create a product that is both functional and adaptable. The journey from raw materials to the final product is a testament to human ingenuity and the relentless pursuit of quality. With continuous advancements in manufacturing processes, we can expect even more advanced and sustainable PVC coated wire solutions in the future.