In the realm of construction and industrial applications, wire mesh stands as a versatile and indispensable material, renowned for its strength, durability, and adaptability. As a product expert with years of experience, it's critical to delve into the nuances that make wire mesh a superior choice for myriad uses while optimizing for SEO objectives.
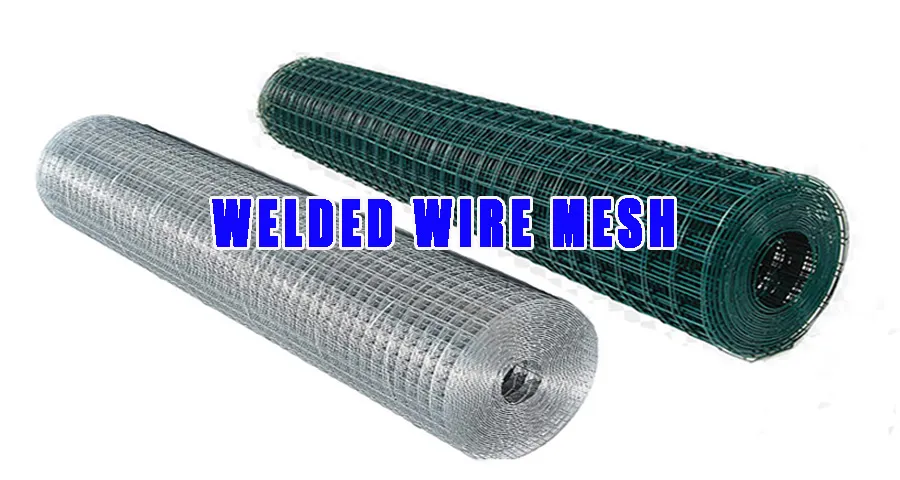
Wire mesh, often fabricated from stainless steel, galvanized steel, or aluminum, is a fabric-like structure made of intersecting metal wires welded or woven into a grid pattern. Its ubiquitous presence is due to its exceptional properties, including robustness, flexibility, and corrosion resistance, thus making it ideal for a wide array of applications from agricultural fencing to high-security installations.
To fully appreciate the utility of wire mesh, one must explore its various specifications and the roles they play in different contexts.
One principal factor is the mesh size, which directly impacts the strength and transparency of the mesh. A finer mesh size offers a high level of filtration and is often used in sieving and sifting applications, ensuring precision in industries like pharmaceuticals and food processing. Conversely, a larger mesh size provides excellent structural integrity suitable for construction uses such as reinforcing concrete or acting as a guard screen, preventing debris from falling on workers and tools.
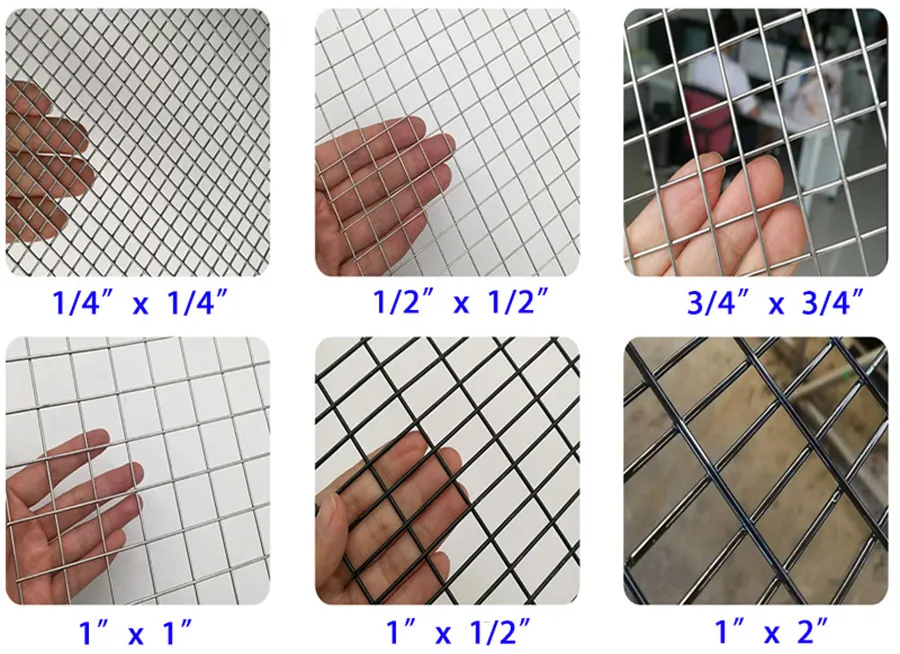
Wire diameter, another critical attribute, dictates the durability and flexibility of the wire mesh. Thicker wires provide enhanced strength and longevity, essential for demanding environments like mining or heavy-duty fencing. In contrast, thinner wires offer a more lightweight solution suitable for artistic architectural designs and intricate detailing.
wire mesh
For those entrenched in the field, understanding the differences between woven and welded wire mesh is pivotal. Woven wire mesh, produced akin to fabric, provides elasticity and can absorb stress without breaking, ideal for applications requiring frequent movement or vibration. In contrast, welded wire mesh features stronger intersections, offering enhanced rigidity and making it perfectly suited for static structures and cages.
From an authoritative perspective, the selection of wire mesh should be informed by both environmental considerations and specific project needs. Stainless steel meshes bring unparalleled corrosion resistance in marine and chemical processing industries, while galvanized and coated meshes provide cost-effective alternatives for less corrosive settings. Partnering with reputable manufacturers that adhere to international standards ensures product reliability and adherence to safety regulations.
Ultimately, the trustworthiness of a wire mesh solution is paramount. End-users should prioritize sourcing from suppliers who offer comprehensive support, including engineering consultations, custom fabrication options, and prompt delivery services. Such attributes, coupled with positive customer testimonials and a robust online presence, bolster a company's reputation as a reliable provider of wire mesh solutions.
In conclusion, wire mesh is more than just a construction staple; it is a testament to engineering excellence, enhanced by its adaptability and resilience. By focusing on quality, specifications, and trusted suppliers, businesses can achieve optimal results in their projects, cementing wire mesh's role as an irreplaceable component in modern industry.