Metal mesh, a versatile and durable material, has become essential in various industrial and architectural applications. Its unique combination of strength, flexibility, and aesthetic appeal makes it suitable for an array of uses, ranging from industrial filtration to modern architectural designs. The rising popularity and broad utility of metal mesh underscore the importance of selecting the right type for specific applications, ensuring optimal performance and longevity.
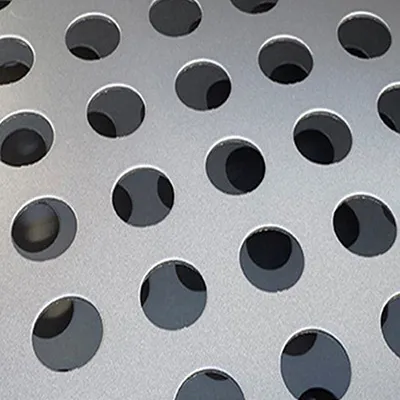
A crucial aspect of metal mesh is its composition and manufacturing process. Typically made from stainless steel, copper, aluminum, or brass, metal mesh is produced using techniques such as welding, knitting, or weaving. Each method imparts distinct characteristics to the mesh,
influencing its strength, flexibility, and appearance. For instance, welded metal mesh is known for its rigidity and strength, making it ideal for construction applications that require robust support structures. On the other hand, woven or knitted meshes offer higher flexibility, which is beneficial in design applications where intricate forms or movements are required.
The applications of metal mesh are vast and varied. In industrial settings, metal mesh is often utilized in filtration systems to separate particles from liquids or gases, a process critical in industries such as oil and gas, chemical processing, and food production. Its superior resistance to high temperatures and corrosive environments makes it a preferred choice over other materials. Additionally, metal meshes are used in conveyor belts, offering resilience and reliability under heavy loads and rigorous conditions.
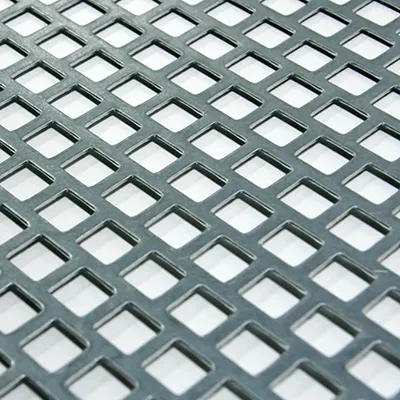
In the realm of architecture, metal mesh has been embraced for both its functional and aesthetic properties. Architects and designers leverage its versatility to create facades, interior panels, and sunshades that not only enhance the visual appeal of buildings but also contribute to energy efficiency. Metal mesh facades, for example, can diffuse natural light and reduce heat gain, thereby enhancing the building's overall environmental performance.
metal mesh
Beyond industrial and architectural uses, metal mesh finds applications in safety and security. It is used in the production of protective gear, such as gloves and aprons, owing to its capability to withstand cuts and abrasions. Furthermore, metal mesh is employed in security screens and fencing, providing a high level of visibility while serving as a robust barrier against intrusions.
Choosing the right metal mesh involves considering factors such as mesh size, wire diameter, and the material's intrinsic properties. Mesh size and wire diameter determine the mesh's permeability and strength and are crucial specifications for achieving the desired filtration or reinforcement objectives. The choice of material impacts the mesh's durability and resistance to environmental conditions, key considerations in applications exposed to external elements.
Innovations in metal mesh technology continue to broaden its applications and improve its performance. Advanced coatings and treatments enhance its corrosion resistance and aesthetic appeal, while new alloy compositions expand its capabilities in extreme conditions. As technology progresses, metal mesh is expected to play an increasingly integral role in industries focusing on sustainability and efficiency.
In summary, metal mesh stands out as a critical component across a multitude of industries due to its versatile functionality and robust nature. Choosing the appropriate type of metal mesh and understanding its material characteristics and production methods are paramount in optimizing its application. As both technological advancements and industry demands evolve, metal mesh's relevance and utility are poised to expand, reaffirming its importance as a reliable, efficient solution.